The Role of Quality Control in Project Management
In today's fast-paced business environment, project management plays a vital role in ensuring that projects are completed on time, within budget, and to the required quality standards. One of the key components of successful project management is Quality Control (QC). Quality control can be defined as the process through which a business ensures that product quality meets the specified requirements, leading to high customer satisfaction and robust project outcomes. With effective QC strategies, project managers can significantly reduce risks, enhance project performance, and optimize resource utilization.
Implementing Quality Control is not merely a checkbox activity; it involves understanding processes, applying the right tools, and fostering a culture of quality. This article discusses the theoretical foundations and practical applications of Quality Control in project management, equipping you with effective strategies to ensure project success.
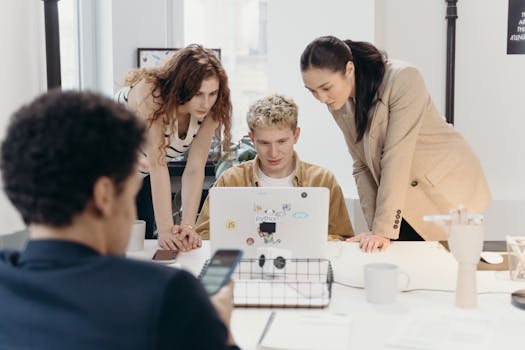
π Key Conceptsβ
What is Quality Control?β
Quality Control is a strategic component of project management that focuses on the identification and elimination of defects in products, processes, and services. The primary goal of QC is to ensure that the output meets the desired quality standards defined at the projectβs onset. Commonly used tools for quality control include statistical process control (SPC), control charts, and fault tree analysis.
The Importance of Quality Control in Project Managementβ
- Customer Satisfaction: Delivering high-quality products increases customer loyalty and satisfaction, which are crucial for long-term success.
- Cost Efficiency: By identifying issues early and preventing defects, organizations can reduce waste and lower rework costs.
- Improved Reputation: Consistently delivering quality projects strengthens the organization's brand and reputation in the market.
- Compliance and Risk Management: Quality Control ensures adherence to regulatory requirements and minimizes risks associated with poor quality.
Quality Control Frameworks and Techniquesβ
Several frameworks and methods are widely used in Quality Control. These include:
- Total Quality Management (TQM): A management approach advocating for continuous improvement across all functions of the organization.
- Six Sigma: A data-driven methodology that strives for near perfection in project delivery by minimizing defects (3.4 defects per million opportunities).
- Lean Management: Focuses on maximizing customer value while minimizing waste, resulting in a more efficient project process.
Quality Control vs. Quality Assuranceβ
Itβs critical to distinguish between Quality Control (QC) and Quality Assurance (QA). While QC focuses on the evaluation of outputs and identification of defects, QA emphasizes the processes involved in project execution, ensuring that they meet quality standards throughout the project lifecycle.
π― How to Applyβ
Step 1: Define Quality Standardsβ
π Define Quality Standards: Start by establishing clear and measurable quality standards for your project. Involve stakeholders to create a shared understanding of quality expectations. Use tools like SMART criteria (Specific, Measurable, Achievable, Relevant, Time-bound) to set goals.
Example: For a software development project, a quality standard might define that the application should have a maximum of 2% bugs reported in the live environment within the first three months of launch.
Step 2: Develop Quality Control Processesβ
ποΈ Develop Quality Control Processes: Create detailed processes that will govern the implementation of QC measures. This includes defining the stages at which quality checks will occur and who will be responsible for them.
Example: Establish a QC checklist that needs to be completed before each project milestone. This could include key evaluations such as requirements validation, design reviews, and test plan approvals.
Step 3: Monitor and Measure Qualityβ
π Monitor and Measure Quality: Set up metrics that allow you to monitor the quality of the outputs and track progress against your quality standards. Tools such as control charts can help you visualize quality trends over time.
Example: If you're managing a construction project, you could implement weekly inspections using a standard checklist to identify and document compliance with safety and quality standards.
Step 4: Implement Corrective Actionsβ
π Implement Corrective Actions: When defects or deviations from quality standards are identified, itβs essential to have a responsive plan in place. This might involve brainstorming sessions to determine root causes and corrective measures to address issues.
Example: If a product batch shows a higher than acceptable error rate, form a cross-functional team to analyze production processes and implement immediate changes to rectify the problem.
Step 5: Continuous Improvementβ
π― Continuous Improvement: Adopt a culture of continual tracking and improvement in project quality. Collect feedback from stakeholders and create a cycle of ongoing refinement using Plan-Do-Check-Act (PDCA) cycles.
Example: After each project completion, conduct a retrospective to analyze successes and failures related to quality control. Use this learning to shape future project standards.
Practical Example: Implementing QC in Software Developmentβ
Letβs look at a real-life scenario in the software industry where effective Quality Control strategies were implemented.
Case Study: Implementing Quality Control in XYZ Software Company
-
Project Overview: XYZ Software Company undertook a project to develop a customer relationship management (CRM) system to enhance user experience.
-
Quality Standards Definition: Early on, the project manager defined quality standards with stakeholders, ensuring the system had a 99.9% uptime and a user satisfaction score of at least 85% upon release.
-
Control Processes: QC processes included daily stand-up meetings, weekly integration testing, and a final user acceptance testing phase before launch.
-
Monitoring and Measurement: The team used automated testing tools and error tracking software to monitor bugs and system performance continually.
-
Corrective Actions: A feature was identified as causing users difficulties during beta testing; the team swiftly iterated on user feedback, leading to a redesign that improved usability.
-
Continuous Improvement: Regular sprints and retrospectives were held to assess what worked and what didnβt, ensuring that lessons learned informed future projects.
Consequently, XYZ Software Company launched the CRM successfully, achieving a user satisfaction score of 90% and a significant reduction in post-launch bugs.
Manage projects with Workfeed
Workfeed is the project management platform that helps small teams move faster and make more progress than they ever thought possible.
Get Started - It's FREE* No credit card required
π οΈ Frequently Asked Questionsβ
Here are some frequently asked questions about "The Role of Quality Control in Project Management".
π Conclusion
In conclusion, integrating Quality Control strategies in project management is essential for delivering high-quality projects. By defining quality standards, developing effective processes, monitoring outcomes, implementing corrective actions, and fostering a culture of continuous improvement, project managers can achieve outstanding results. Embracing these practices not only enhances customer satisfaction but also strengthens the overall project delivery framework. Remember, quality is not just an act but a habit that shapes project successβlet it guide your projects towards excellence! π