How to Implement a Quality Management System (QMS)
In today's competitive business landscape, having a robust Quality Management System (QMS) is crucial for organizations aiming to deliver high-quality products and services. A QMS enables businesses to streamline processes, enhance customer satisfaction, and comply with regulatory standards. This article presents effective strategies for implementing a QMS that not only meet industry standards but also foster a culture of continuous improvement within your organization.
Implementing a QMS can initially seem daunting, but breaking it down into manageable steps can make the process more feasible. From understanding the core concepts to applying practical strategies, this guide aims to equip you with the necessary tools and knowledge to successfully introduce a QMS in your organization.
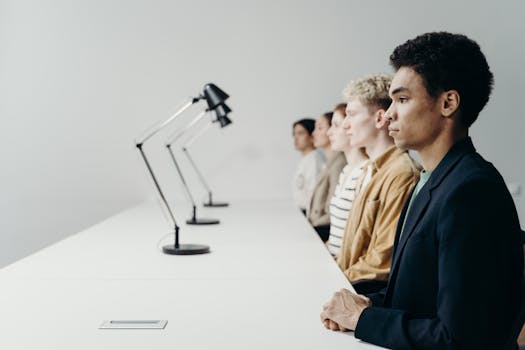
π Key Conceptsβ
Understanding the foundational principles of a QMS is essential to its effective implementation. Here are the key concepts that underpin a successful Quality Management System:
-
Quality Policy and Objectives: π
A quality policy sets the direction and purpose of the QMS. It should align with the overall business goals. Objectives should be Specific, Measurable, Achievable, Relevant, and Time-bound (SMART). -
Customer Focus: π₯
The primary goal of any business should be to meet or exceed customer expectations. Understanding customer needs and enhancing customer satisfaction should be central to your QMS. -
Process Approach: π
A QMS should focus on processes rather than just outcomes. Identify, document, and manage all processes involved in delivering products/services, ensuring that they are effective and efficient. -
Continuous Improvement: π
An effective QMS is not a one-time project but a commitment to ongoing refinement of processes. Use tools like the Plan-Do-Check-Act (PDCA) cycle to foster a culture of continual enhancement. -
Employee Involvement: π©βπΌ
Every employee must understand their role in the QMS and how they can contribute to the quality objectives. Training and involvement can enhance motivation and engagement. -
Data-Driven Decision Making: π
For effective performance assessment, utilize data to guide decisions. Monitoring and analyzing performance indicators will help identify areas for improvement. -
Supplier Quality Management: ποΈ
Ensure that your suppliers meet your quality standards. Setting expectations and regularly assessing supplier performance is critical within the QMS framework. -
Compliance and Risk Management: βοΈ
A QMS should also include procedures for complying with relevant regulations and addressing risks and opportunities that could impact quality.
π― How to Applyβ
Now that you understand key concepts, letβs look at how to apply these theories in real-life scenarios. Hereβs a comprehensive handbook detailing the steps for implementing a QMS.
π Step 1: Define the Quality Management Frameworkβ
Identify what kind of QMS your organization will implement. This involves assessing current processes, identifying gaps, and aligning them with customer needs and business objectives.
- Example: In a manufacturing company, conduct a SWOT analysis to understand strengths and weaknesses in current quality processes.
π Step 2: Develop Quality Policies and Objectivesβ
Draft a quality policy that outlines the commitment to quality. Set SMART objectives that are aligned with this policy.
- Example: "Increase customer satisfaction by 15% within the next year through feedback surveys and responsive actions."
π Step 3: Engage Employeesβ
Communicate the QMS goals and involve employees in the implementation process. Hold training sessions to explain how they can contribute to quality objectives.
- Example: Organize workshops and provide training materials that detail their role in the QMS.
π Step 4: Document Processesβ
All processes must be documented, including quality procedures, work instructions, and records. This helps standardize operations and ensure consistency.
- Example: Create a process map for product development, detailing every step from ideation to delivery.
π Step 5: Implement the QMSβ
Begin the rollout of your QMS. Assign roles and responsibilities, ensuring everyone understands their tasks.
- Example: Adopt a phased approach, starting with one department, like production, and gradually implementing across other areas.
π Step 6: Monitor Performanceβ
Establish key performance indicators (KPIs) to track the effectiveness of the QMS. Use data to assess whether quality objectives are being met.
- Example: Monthly reviews of defect rates in products to determine if there is a decrease in errors.
π Step 7: Conduct Auditsβ
Regular internal audits will help ensure compliance with the QMS standards and identify areas needing improvement.
- Example: A quarterly audit on the documentation process to ensure records are being maintained correctly.
π Step 8: Focus on Continuous Improvementβ
Utilize the PDCA cycle for ongoing refinement of processes. Encourage a culture where employees can suggest improvements.
- Example: Schedule regular feedback sessions where team members can propose changes to current processes based on their experiences.
π Step 9: Gather Customer Feedbackβ
Solicit feedback from customers regularly to gauge their satisfaction levels and areas for improvement.
- Example: Use online surveys post-purchase to gather insights into customer experiences and perceptions of quality.
π Step 10: Review and Adaptβ
Regularly revisit the QMS policies and objectives to ensure they remain relevant to the changing business environment and customer demands.
- Example: Annual review of the QMS with stakeholders to adapt strategies based on new market trends or customer feedback.
Manage projects with Workfeed
Workfeed is the project management platform that helps small teams move faster and make more progress than they ever thought possible.
Get Started - It's FREE* No credit card required
π οΈ Frequently Asked Questionsβ
Here are some frequently asked questions about "How to Implement a Quality Management System (QMS)".
π Conclusionβ
Implementing a Quality Management System (QMS) can transform your organization by enhancing operational efficiency and customer satisfaction. The journey may be challenging, but by following structured strategies and engaging employees at every step, you can create a culture of quality and continuous improvement. π As the business world evolves, a robust QMS will position your organization to respond effectively to changing demands, ensuring long-term success. Remember, quality is not just a goal; itβs a journey. Letβs embark on this journey together!