Effective Strategies for Continuous Improvement Tools and Techniques
Continuous Improvement (CI) is a management philosophy that aims to enhance processes, products, and services through gradual, incremental improvements. It is founded on the belief that even small changes can yield significant enhancements in performance, efficiency, and customer satisfaction. By nourishing a culture of reflection and adaptation, organizations can identify inefficiencies and bottlenecks, driving better outcomes over time.
In todayβs fast-paced business environment, adopting CI tools and techniques is more vital than ever. Not only can they help organizations maintain competitive advantages, but they also foster a proactive approach to change and innovation. This article delves into effective strategies for continuous improvement, discussing key concepts and practical applications that can be implemented across various contexts.
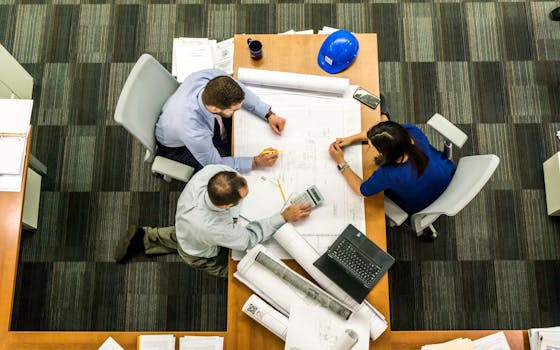
π Key Conceptsβ
π Continuous Improvement Practicesβ
Continuous Improvement involves several methodologies and frameworks, including Lean, Six Sigma, and Total Quality Management (TQM). Though each approach has its distinctive traits, they share a common goal: improving efficiency and quality.
-
Lean focuses on eliminating waste and enhancing flow. The principles prioritize value from the customersβ perspective.
-
Six Sigma employs statistical methods to reduce defects and variance, targeting process improvement through data analysis.
-
Total Quality Management (TQM) emphasizes long-term success through customer satisfaction, employee involvement, and a systematic approach to improve processes.
π PDCA Cycleβ
The Plan-Do-Check-Act (PDCA) cycle is a foundational framework in continuous improvement. This cycle consists of four stages:
- Plan: Identify the problem and develop a strategy for improvement.
- Do: Implement the plan on a small scale.
- Check: Analyze the results and evaluate the effectiveness of the approach.
- Act: Standardize the improvement if successful or refine the plan for further testing.
Using this iterative process helps organizations adapt quickly and learn from their experiences.
π Key CI Toolsβ
Here are some essential continuous improvement tools to consider:
-
5 Whys: A simple yet effective technique used to uncover the root cause of a problem by asking "why" multiple times.
-
Value Stream Mapping: A visualization tool that helps identify waste in processes and highlights areas for improvement.
-
Kaizen: A Japanese term meaning "change for better," Kaizen focuses on small, continuous changes that result in significant improvements over time.
-
Benchmarking: Comparing organizational practices to industry standards or competitors to identify areas for improvement.
-
Fishbone Diagram: A visual representation that categorizes potential causes of a problem, helping teams to brainstorm solutions systematically.
π― How to Applyβ
Implementing continuous improvement tools and techniques can seem daunting, but with a structured approach, organizations can effectively foster a culture of CI. Here's a practical handbook:
π Step 1: Assess Current Processesβ
Assess: Conduct an assessment of current practices. Hold focus groups and gather feedback from employees to understand pain points in processes.
- ποΈ Example: A manufacturing company can review production lines for inefficiencies by collecting data on cycle times and wait times.
π Step 2: Identify Improvement Opportunitiesβ
Identify: Utilize tools like Value Stream Mapping and 5 Whys to highlight specific areas needing improvement.
- π Example: By mapping out the value stream, teams might discover that excessive inventory leads to delays, prompting an initiative to implement Just-in-Time (JIT) inventory practices.
π Step 3: Develop Action Plansβ
Develop: Create actionable plans to tackle identified issues. Involve team members for diverse perspectives and engagement.
- π― Example: Using the PDCA cycle, the team can outline a pilot plan to reduce waiting times on the production floor.
π Step 4: Implement Changesβ
Implement: Execute the plan on a small scale. Ensure that all team members are aware of their roles and responsibilities in the new process.
- π Example: The manufacturing team might implement a new scheduling system aimed at optimizing workforce allocation.
π Step 5: Measure Resultsβ
Measure: Evaluate the outcomes against the objectives set in the planning stage. Use metrics such as cycle time and quality scores.
- π Example: If cycle times decreased from 15 minutes to 10 minutes, this successful outcome should be documented and celebrated.
π Step 6: Standardize Successful Improvementsβ
Standardize: If the changes yield positive results, implement them at a larger scale and update standard operating procedures (SOPs).
- π Example: After successful pilot tests, the new scheduling system can be rolled out across all shifts in the manufacturing unit.
π Step 7: Foster a Continuous Improvement Cultureβ
Foster: Encourage employees to think critically and share ideas for improvements regularly. Reward contributions to motivate ongoing participation.
- π Example: Monthly CI meetings can be held to share successes, discuss new challenges, and explore innovative improvements.
Manage projects with Workfeed
Workfeed is the project management platform that helps small teams move faster and make more progress than they ever thought possible.
Get Started - It's FREE* No credit card required
π οΈ Frequently Asked Questionsβ
Here are some frequently asked questions about "Effective Strategies for Continuous Improvement Tools and Techniques".
π Conclusionβ
In conclusion, continuous improvement is not just a set of techniques but rather a mindset that organizations must cultivate. By employing effective tools and embracing strategic frameworks like the PDCA cycle, companies can achieve significant progress in enhancing their processes. Implementing these improvements requires commitment, collaboration, and creativity from the entire team.
As organizations adapt and evolve, fostering a culture that values feedback and innovation will ensure ongoing success. With the right strategies and commitment, continuous improvement becomes an integral part of the organizational DNA, leading to sustained excellence and customer satisfaction. Let's embrace the journey of continuous improvement together! π